

FLV Visits Mercedes Benz Technology Center for Vehicle Safety
By special kindness of Mercedes Benz we could visit the very new vehicle safety test center in the city of Sindelfingen in Germany.
We were received and guided in our tour by Engineer Andreas Kramer, who we are very thankful for his attention and information given about the test center during our visit.
Joining us to this visit also present Mr. Jens Wolking, Business Development Manager from Kistler. The data acquisition systems in the Mercedes Benz center are supplied by Kistler, utilizing in dummy technology.

The new Mercedes Benz Technology Center for Vehicle Safety
Photo Daimler – Global Media Center
The initial planning for the center construction started in 2012. The works began in April 2014, with the first effective test in September 2016
The building is impressive by its size and architecture. With a total area of 55,000 sqmt, the center has what is the most advanced technology and equipment for vehicle safety testing, including electric vehicles, trucks and even tractors.
Safety is present in every detail. Close to the area for electrical vehicle testing was built a huge uncovered pool. In case of fire in the lithium batteries, the test vehicle can be quickly moved out the building by a special tractor and submerged in the pool extinguishing the fire.
The covered free space area for tests is enormous. Many test tracks e capability to perform any kind of vehicle crash test at any impact angle.
From the test center elevated tower it is possible to visualize the entire test area, enabling complete operation control with total safety.
A visit to the Safety Center requires a certain level of physical fitness to cover the distances between the testing areas and laboratories. Some times small electrical vehicles, nicknamed “ants” are utilized. But the majority of the operation personnel cover the distance on foot.
“It is part of the admission process to work in the center, a previous physical fitness evaluation from the candidate. We need to make sure that the person is in good shape to the required walks during the work period”- says Kramer.

The test center has four tracks for tests, each one can be operated independently
Photo Daimler – Global Media Center
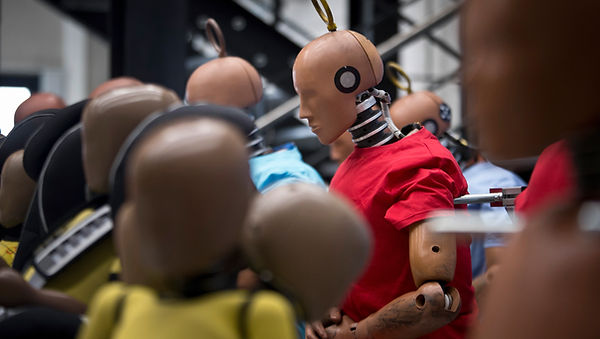
Dummy Lab – A total of 120 test dummies are prepared under controlled temperature conditions. Some dummies could reach to 220 measuring points at a cost of 700,000 Euros per dummy
Photo Daimler – Global Media Ce
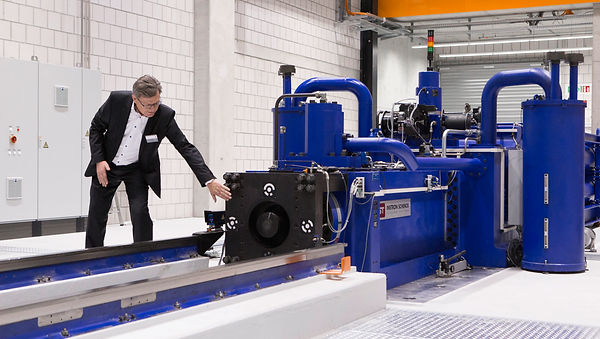
In the picture the acceleration sled Hidropuls from IST Instron (represented in Brazil by FLV), one of the four existing sleds in the Mercedes Benz Technology Center in Sindelfingen
Photo Daimler – Global Media Center
Key Facts
-
Construction: autumn 2013 – autumn 2016
-
Location: in the Mercedes-Benz Technology Center (MTC) in Sindelfingen
-
Investment: three-figure sum in millions
-
Possible crash configurations: around 70 different configurations for cars and trucks, incl. frontal crash (with varying degrees of overlap), rear impact, side impact with movable barriers and lateral post impact, rollover test and vehicle-to-vehicle crash
-
Documentation: using high-speed cameras (up to 1000 images per second), also from below (glass-covered filming pits)
-
Major test facilities: interior crash hall with angled tracks and PRE-SAFE® area, four crash tracks, sled test area, gradient/rollover ramp for rollover tests, test stand for head impact tests
-
Special features: now makes crash tests possible in which the vehicles drive to the obstacle under their own power (also electric and fuel cell vehicles), simulation of real accidents including emergency braking, one rotating and one freely movable crash block plus three stationary blocks, hovercraft for smooth transport of vehicle bodies for sled tests, use of drones for safety monitoring in the crash hall, integrated store for dummies and sled body shells, highly precise, automated measuring systems (incl. coordinate measuring system and surface scan)
-
Building dimensions: 170 m x 279 m x 23 m
-
Area: 55,000 m2
-
Longest crash track length: over 200 m
-
Dimensions of the unsupported area of the crash hall: 90 m x 90 m
-
Climate control: use of waste heat from the adjacent climatic wind tunnels